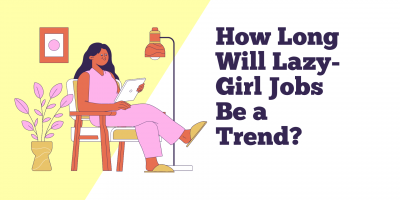
How Long Will Lazy-Girl Jobs Be a Trend?
The “lazy girl jobs” movement isn’t about laziness at all. It’s about drawing a line between self-care and overexertion.
While safety standards in the workplace have generally improved across industries, many companies still struggle to achieve a sustained standard in their safety performance.
In fact, a worker is injured on the job every seven seconds in the United States.
That’s over 4.5 million work injuries each year. In 2021, there were 4,472 preventable injury-related deaths among workers, a 9% increase from the year before.
However, the most disheartening fact is that most of these accidents are preventable.
An employer’s responsibility is to identify and prevent workplace hazards, and one of the most effective ways to achieve it is through regular safety OSHA compliance training combined with Environment, Health and Safety (EHS) software.
Many businesses are reluctant to invest in safety measures.
Employers may view OSHA regulations as burdensome and costly, and they may not believe they are necessary for their specific industry.
However, the cost of workplace injuries and fatalities is far greater than the cost of preventing them. In addition to the human cost, businesses also face financial losses due to lost productivity, medical expenses, and legal fees.
This article explores the intricate web of workplace safety, where regulations, human behavior, and corporate responsibility converge to define the very essence of a secure and thriving work environment.
Workplace safety is the practice of protecting employees from illness and injury in their workplace. It begins with developing a company Environmental, Safety, and Health (EHS) policy statement and implementing a workplace safety plan and program.
Some common workplace safety concerns include ergonomics, hazardous chemicals, noise pollution, weather-related hazards, or mechanical problems.
While workplace safety is common today, that wasn’t always the case. Accidents were seen as an unfortunate but unavoidable part of doing business for a large part of history.
That changed in 1970 when President Richard Nixon signed the Occupational Safety and Health Act (OSH) into law. The OSH Act is one of the most important workplace safety legislation in American history.
Since its passage, workplace fatalities have been reduced by over 60%.
So, what is occupational safety and health?
Occupational safety and health (OSH) is a multidisciplinary field concerned with workers’ safety, health, and welfare.
Occupational health focuses on three main objectives:
Following the OSH Act, Congress established two agencies, the Occupational Safety and Health Administration (OSHA) and the National Institute for Occupational Safety and Health (NIOSH).
OSHA is a federal agency responsible for enforcing the OSH Act in private-sector workplaces.
According to OSHA, workplace safety involves actively safeguarding employees from job-related illnesses and injuries. This definition extends beyond mere reaction; it strongly emphasizes proactively averting accidents and harm before they occur.
The spectrum of OSHA’s regulations encompasses a wide array of workplace safety aspects, from hazard identification and control measures to employee training and recordkeeping requirements.
OSHA’s definition of workplace safety is important because it provides a clear framework for employers and employees to understand their responsibilities in creating and maintaining a safe workplace.
The standards set by OSHA are the minimum safety requirements that companies must follow. Therefore, these standards are legally binding obligations for organizations.
While some states have opted to establish their own occupational enforcement agencies, these agencies must, at the very least, meet the federal standards set by OSHA. Although federal intervention in such cases is rare, it remains a possibility.
Compliance with OSHA regulations is an absolute necessity.
Inspectors responsible for ensuring compliance have the authority to issue citations for any violations they may uncover.
It’s important to note that the OSHA scrutiny and enforcement level becomes more rigid as industries become more industrial.
However, it’s worth mentioning that OSHA regulations do not universally apply to all industries or jurisdictions.
Specific sectors, such as the mining industry, are governed by the Department of Labor’s Mine Safety and Health Administration (DOL-MSHA). At the same time, the various branches of the U.S. military have their own distinct safety regulations.
In the realm of safety guidelines, there’s no one-size-fits-all solution.
Workplace injuries and illnesses happen across various settings, from factories and healthcare facilities to offices and service industries. Even workers on the move, like salespeople, can face risks.
OSHA provides recommended practices that apply universally, spanning different sectors, hazard types, work environments, and organization sizes.
These practices revolve around seven core elements, forming an integrated system:
These recommended practices can be further adapted to the specific needs of each workplace.
A safety and health program should also evolve over time. This may involve experimenting with different approaches, evaluating the results, and modifying the program as needed.
The aims of occupational health and safety are to protect workers from workplace hazards and promote a safe and healthy working environment. While all jobs have certain risks, some are inherently more dangerous than others.
The top 5 occupations with the largest number of fatalities in 2021 were:
Typical workplace hazards can be categorized into several major groups. Below are the most common workplace hazards, along with the corresponding OSHA compliance requirements:
The list of workplace injuries shows that no business is immune to the risk of employee injury, regardless of size or industry.
So, how can business owners ensure that they are managing this risk effectively and protecting their workers?
By law, employers have a responsibility to provide a safe workplace.
This means complying with all applicable OSHA standards designed to protect workers.
For example, one of the most well-known responsibilities for employers is to exhibit the official OSHA “It’s the Law” poster that provides information about rights and responsibilities.
Employers must also identify and correct any safety hazards in the workplace, and they must provide employees with the training and equipment they need to work safely.
Moreover, the OSH Act emphasizes that employers should prioritize hazard prevention or reduction through changes in working conditions rather than solely relying on personal protective equipment like masks or gloves.
Regarding OSHA compliance, it’s not just about ticking boxes on a checklist; it’s about creating a safe and healthy work environment for your employees.
A safety-centric culture also has an impact on the mental and emotional well-being of employees. When workers feel safe and secure in their workplace, they experience lower stress levels and anxiety related to safety concerns.
Most HR professionals are primarily aligned with traditional workforce management activities, such as recruitment, performance management, leave management, benefits management, and improving the whole employee experience.
However, ensuring a safe working environment is equally vital for employee well-being, so HR professionals must understand how secure their workspaces are for guaranteed employee health.
What often goes unnoticed is the complexity of maintaining a workspace that adheres to the 180 federal laws governing employee health and safety. Additionally, state-level regulations further increase the compliance burden.
Complying with these legal requirements can be time-consuming, but it is undeniably crucial. Workplace illnesses and injuries account for roughly 3% of the workforce being out-of-commission at any given time, resulting in an annual cost of approximately $171 billion.
The role of HR in ensuring workplace health and safety is multifaceted, with both direct and indirect responsibilities.
Direct responsibilities come into play when:
However, HR’s influence on workplace health and safety extends beyond these direct responsibilities. Indirect responsibilities include:
Therefore, HR professionals play a pivotal role in navigating this intricate regulatory landscape to protect both employees and the organization as a whole.
When an OSHA inspector comes for a visit, it often causes fear or even panic, especially among managers who are new to the process. However, it’s interesting to note that many OSHA inspections actually lead to significant improvements in a company’s operations.
According to research, OSHA’s random inspections of high-risk workplaces resulted in a 9% decrease in injuries that led to workers’ compensation claims in the four years following the inspection. Each inspection saved employers around $350,000 in wage replacement and medical costs on average.
So, what triggers an OSHA inspection?
An OSHA inspection can be initiated in several ways:
The opening conference is a brief meeting between the OSHA inspector and the employer or their representative.
The inspector will explain the purpose of the inspection, the scope of the inspection, and the rights of the employer and employees. The employer will select a representative to accompany the inspector during the inspection.
The walkaround is the main part of the inspection. The inspector will tour the workplace and look for hazards that violate OSHA regulations.
Inspectors also often interview employees to gather information about workplace conditions, safety procedures, and any concerns they may have.
They could also review safety records and take measurements or photographs of the workplace.
The closing conference is a meeting between the inspector and the employer or their representative to discuss the findings of the inspection.
The inspector will explain any violations that have been found and discuss the procedures that need to be taken. The employer will have the opportunity to contest any violations.
If the inspector finds any violations of OSHA regulations, they will issue a citation. A citation is a written notice that identifies the violation and specifies the corrective action that needs to be taken, along with a monetary penalty.
The penalty amount depends on the severity of the violation and the employer’s compliance history. For example, a serious violation with a history of non-compliance could result in a penalty of up to $136,532.
There are four main types of citations:
Employers can prepare for OSHA inspections by keeping a good record of safety and health training and familiarizing themselves with OSHA regulations that apply to their workplace.
When it comes to ensuring workplace safety and making it a part of a company’s DNA, organizations must engage with everyone involved, from top executives to regular employees, in open and ongoing conversations.
Typically, in large industrial companies, especially those dealing with workplace hazards, significant efforts and resources are devoted to reducing injuries and incidents. These companies usually set up comprehensive health, safety, and environment (HSE) management systems, often including HSE incident reporting in their annual reports.
However, despite initial improvements, many organizations hit a roadblock in their safety progress.
This plateau often happens when organizations attempt to shape a safety-conscious culture by placing excessive emphasis on tools and processes while failing to address the mindsets of their employees that influence personal safety behaviors and interactions.
Interestingly, McKinsey’s research shows that organizations achieving exceptionally high safety standards tend to focus not only on “hard” practices like implementing incentive systems to reinforce safe behaviors but also on “soft” practices.
These include encouraging employees to take ownership of safety issues, lead safety initiatives, and embrace strong safety values.
To make a workplace safety program genuinely effective, employees must actively participate in its creation and execution. Their firsthand knowledge and insights are invaluable in designing safety protocols that work.
Ultimately, safety in the workplace isn’t a one-sided responsibility – it’s a shared commitment that both employers and workers must uphold.
Creating an OSHA compliance checklist is a crucial step for ensuring workplace safety and adhering to the regulations set by the Occupational Safety and Health Administration (OSHA).
Below is an example of an OSHA compliance checklist for some of the most common hazards in the workplace.
Hazard Communication |
- Are all hazardous materials labeled with their chemical name, physical and health hazards, and emergency procedures? - Are Safety Data Sheets (SDSs) available for all hazardous materials? - Are employees trained on the hazards of the chemicals they work with? |
Fall Protection |
- Are employees working at heights 6 feet or more above the ground protected from falls? - Are fall protection measures implemented (e.g., guardrails, safety nets, personal fall arrest systems)? - Are fall hazards identified in the workplace? |
Electrical Safety |
- Are all electrical cords and equipment in good condition? - Are electrical outlets and switches properly grounded? - Are employees trained on electrical safety? |
Machine Guarding |
- Are all moving parts of machinery guarded? - Can employees reach moving parts without removing guards? - Are employees trained on the proper use of machinery? |
Emergency Action Plan |
- Does the workplace have an emergency action plan? - Is the plan posted in a visible location? - Are employees trained on the emergency action plan? |
Fire Prevention |
- Are fire extinguishers and fire alarms in good working order? - Are employees trained on how to use fire extinguishers? - Are fire exits clearly marked? - Are fire drills conducted with established evacuation routes? |
First Aid and Medical Services |
- Is there a well-stocked first aid kit available? - Are designated personnel trained in first aid? - Are procedures in place for reporting and recording injuries? |
This is just a sample checklist, and the specific requirements will vary depending on the industry and the specific hazards present in the workplace.
Workers are only human, and humans make mistakes.
Regardless of the task, there will come a time when an individual becomes fatigued, loses interest, or becomes distracted.
Consequently, mistakes are bound to happen.
Effective safety programs acknowledge this reality and implement numerous backup systems to prevent errors from leading to accidents or fatalities.
One effective way to manage workplace safety is to implement a Safety and Health Management System (SHMS).
SHMSs are cyclical processes that involve planning, doing, checking, and acting, sometimes called the “Deming Wheel.” This iterative approach allows continuous improvement and ensures that safety is always prioritized.
SHMSs should also include protocols for investigating incidents, such as near misses and close calls. These investigations can help identify the root causes of incidents and prevent them from happening in the future.
What’s more, this system should allow employees to report hazards and concerns without fear of retaliation or discrimination.
Finally, organizations should create a culture of safety where safety is a priority at all levels of the organization.
Injury rates, often referred to as “OSHA recordables,” serve as crucial metrics that reflect the actual experiences of the workforce.
For a long time, it was believed that preventing minor injuries would also prevent the occurrence of more severe ones. If injury rates are low, there’s no real reason for concern, right?
Well, “OSHA recordables” are lagging indicators, meaning they only measure past safety performance results. As such, they are not a comprehensive measure of a company’s safety and health management system.
In fact, the factors leading to severe and fatal injuries often follow different paths than those causing the majority of “OSHA recordable” injuries, making it hard to foresee any safety lapses.
A well-known example is the Deepwater Horizon drilling rig incident, where BP executives were present the night before the catastrophic explosion, rewarding the workers for their low injury rate.
Instead, companies should also use leading indicators, such as hazard identification and control, to help identify potential problems before they lead to injuries.
By combining lagging and leading indicators, companies can get a clearer picture of their safety performance and take steps to improve it.
Nevertheless, it is essential to establish concrete goals for injury rates within the company. Instead of fixating on achieving a lower rate, companies should set a target of zero injuries (while emphasizing the mandatory nature of reporting injuries).
One prevalent misconception often arises when corporate leaders evaluate the advantages and disadvantages of occupational health and safety.
Namely, many business leaders hold an implicit but baseless belief that there’s a trade-off between profits and the expenses required to maintain a safe workplace.
However, businesses can be safe and successful at the same time.
In fact, research shows that the top quartile of companies in terms of organizational health have six times fewer safety incidents than the bottom quartile.
So, what are some of the pros and cons of OHS?
Advantages of OHS:
Disadvantages of OHS:
If you believe that working conditions at a workplace are unsafe, you have the right to report the violations to OSHA. Employees can do this anonymously, and their employer is prohibited from retaliating against them for filing a complaint.
So, how to report OSHA violations?
Here are the steps on how to report OSHA violations:
To file a complaint online, go to the OSHA website and click on the “File a Complaint” link. You will need to provide some basic information about yourself and the workplace, as well as the specific violations you are reporting.
To file a complaint by mail, download the OSHA Complaint Form and mail it to the nearest OSHA office. You can also fax the form to the office. To file a complaint by phone, call 1-800-321-OSHA (6742).
In conclusion, while OSHA regulations may seem burdensome to some, they are essential for preventing injuries, saving lives, and protecting businesses from financial losses.
OSHA compliance is not just about adhering to rules; it’s about prioritizing the workforce’s health, wellness, and safety. It’s about recognizing that safety is not a priority but an inherent part of how successful organizations operate.
In the landscape of workplace safety, OSHA compliance remains a cornerstone, providing a framework for organizations to safeguard their employees and uphold their commitment to a safer, healthier, and more productive future.
Senior Content Writer at Shortlister
Browse our curated list of vendors to find the best solution for your needs.
Subscribe to our newsletter for the latest trends, expert tips, and workplace insights!
The “lazy girl jobs” movement isn’t about laziness at all. It’s about drawing a line between self-care and overexertion.
Beyond holiday festivities and annual performances, here’s why December’s focus should be about celebrating human rights in the workplace.
Uncover the rising trends of background checks in the workplace and stay on top of the company’s safety.
With rising gas prices, soaring car maintenance and used vehicle costs, commuting to the office has become a costly burden that drains employees’ finances, productivity, and satisfaction—making commuter benefits a vital solution for employers.
Used by most of the top employee benefits consultants in the US, Shortlister is where you can find, research and select HR and benefits vendors for your clients.
Shortlister helps you reach your ideal prospects. Claim your free account to control your message and receive employer, consultant and health plan leads.